PENGERTIAN
Broaching adalah operasi mesin yang menggunakan alat bergigi, yang disebut bros,ada juga yang menyebutnya mesin pembesar lubang yang biasa digunakan untuk menghilangkan material. bros yang digunakan dalam mesin broaching, kadang-kadang disingkat menjadi memulai pembicaraan mesin. Ini digunakan untuk pekerjaan presisi, terutama untuk bentuk-bentuk aneh. Permukaan Broaching selesai dalam satu kali pekerjaan, biasanya broaching menguntungkan karena digunakan untuk produksi kuantitas tinggi
pisau dibentuk mirip dengan gergaji, kecuali gigi meningkat tinggi atas alat panjang. Selain itu, bros berisi tiga bagian yang berbeda: satu yang awal, satu lagi untuk semi-finishing, dan yang terakhir untuk finishing. Karena semua fitur yang dibuat kompleks maka dibutuhkan tenaga terampil untuk menggunakannya.
bentuk pisau ![clip_image002[15] clip_image002[15]](http://lh4.ggpht.com/_wueh5RRPhOY/TLKYHaq8EqI/AAAAAAAAACI/lhfvPywtFqs/clip_image002%5B15%5D_thumb%5B4%5D.jpg?imgmax=800)
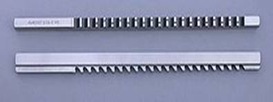
Bahan common rotary broaching meliputi:
* Aluminium
* Brass
* 12L14
* Alloy Steel
* Stainless Steel
* Titanium
FUNGSI
Broaching machine atau mesin pembesar lubang adalah suatu mesin yang berfungsi juga pekerjaan membuang geram-geram, sehingga konstruksi pahatnya mempunyai sederetan gigi-gigi pemotong dengan ukuran kecil di ujung dan semakin besar di pangkal nya. Biasanya, satu suku cadang diselesaikan hanya dalam satu langkah, oleh karena itu ukuran gigi pemotong di pangkal pahat disesuaikan dengan ukuran lubang yang diharapkan.
Walaupun banyak dari jenis mesin ini beroperasi dengan cara menggerakkan alat pembesar lubang dan benda kerja diam, namun sesungguh nya, akan lebih efektif bila dibalik, yakni: benda kerja yang bergerak, alat pembesar lubang diam (stasioner).
JENIS-JENIS BROACHING MACHINE (MESIN PEMBESAR LUBANG)
Berdasarkan cara kerjanya, maka mesin pembesar lubang dapat dikelompokkan menjadi:
1) Pembesar lubang tarik
pahat pembesar lubang digerakkan menembus atau melintasi benda yang stasioner
2) Pembesar lubang dorong
pahat pembesar lubang di dorong menembus atau melintasi benda kerja yang stasioner
3) Pembesar lubang permukaan
4) Pembesar lubang kontinu
benda kerja digerakkan kontinu terhadap pembesar lubang yang stasioner, jalur geraknya dapat lurus maupun melingkar.
Berdasarkan bentuknya broaching machine atau mesin pembesar lubang dibagi menjadi 4
1) MESIN PEMBESAR LUBANG DORONG VERTIKAL
Dibawah ini dapat dilihat gambar contoh pembesar lubang jenis dorong Pada contoh gambar diatas diperlihatkan sebuah roda gigi yang sedang dibuatkan lubang bulat, dimana ternyata proses nya jauh lebih cepat bila dibandingkan dengan kerja nya mesin reamer (mesin perluasan lubang) atau juga dibandingkan dengan kerja nya mesin bor, terutama akurasi hasilnya yang begitu tinggi. Lubang awal sebelum diperbesar dengan alat ini, biasanya merupakan hasil dari mesin gurdi.
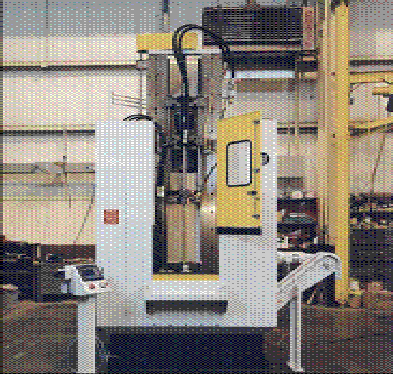
1) MESIN PEMBESAR LUBANG HORIZONTAL
Meskipun mesin pembesar lubang horizontal diperuntukkan bagi pembesaran lubang permukaan, tetapi bisa juga digunakan untuk pembesar lubangsebelah dalam dari benda kerja yang berukuran sedang sampai besar.
Mesin jenis ini mempunyai kecepatan potong antara (3 s/d 12) m/menit dengan kecepatan balik berkisar antara 30 m/menit untuk ukuran yang kecil, tetapi untuk mesin-mesin yang besar(untuk tugas berat), kecepatan potong nya sekitar 60 m/menit dengan ketebalan geram mencapai 6,4 mm dalam setiap langkah
1) MESIN PEMBESAR LUBANG PUTAR
Operasi mesin pembesar lubang putar adalah dengan memasangkan benda kerja yang disanggah pada sebuah meja putar yang bergerak melintasi sebuah alat pembesar lubang fixed. Pembesar lubang ini dibuat dengan ukuran agak pendek, sehingga dapat disetel dan diasah dengan mudah, biasanya digunakan untuk benda-benda yang kecil, seperti untuk membuat bujur sangkar poros distributor, membuat celah, dll.
2) MESIN PEMBESAR LUBANG KONTINU
Benda kerja dijepit secara otomatis sebelum melewati terowongan pemegang tetap dimana alat pembesar lubang berada, dengan adanya mekanisme tertentu, benda kerja dilepaskan oleh sebuah nok untuk kemudian di proses. Efisiensi produksi nya sangat tringgi, sebab operator hanya bertugas untuk memasukkan benda kerja kedalam stasiun pemuatan (loading station).
1. PROSES
Proses ini tergantung pada jenis mesin broaching.
1) Broaching permukaan sangat sederhana baik sebagai benda kerja bergerak terhadap permukaan stasioner bros, atau benda kerja dipegang stasioner sedangkan bros dipindahkan kebalikannya.
2) Broaching internal lebih terlibat. Proses dimulai dengan baik menjepit benda kerja ke workholder dari broaching mesin atau benda kerja diletakkan di atas bola workholder dirancang untuk secara otomatis menyelaraskan benda kerja ke memulai pembroacingan. Lift dari mesin broaching menurunkan pilot bros melalui benda di mana terlibat bros penarik pilot. Lift kemudian melepaskan bagian atas pilot dan penarik menarik bros melalui benda sepenuhnya. Benda kerja kemudian dikeluarkan dari mesin dan bros dinaikkan kembali ke reengage dengan lift. bros biasanya hanya bergerak secara linear, tapi kadang-kadang juga diputar untuk membuat spline spiral atau rifling laras senapan.
Cutting cairan digunakan untuk tiga alasan. Pertama, untuk mendinginkan benda kerja dan bros. Kedua, untuk melumasi permukaan pemotongan. Ketiga, untuk menyiram keripik dari gigi. Dibentengi memotong cairan minyak bumi yang paling umum, namun larut dalam air tugas berat cairan memotong menjadi lebih populer.
2. KEUNTUNGAN DAN KETERBATASAN PEMBESAR LUBANG
Mesin pembesar lubang banyak digunakan untuk operasi pemotongan logam secara massal (mass product), karena sifat dan keunggulan nya sebagai berikut:
1) Pemotongan kasar maupun penyelesaian akhir, dilakukan hanya dalam satu langkah.
2) Waktu penyelesaian pekerjaan sangat cepat (orde detik)
3) Dapat digunakan untuk penyelesaian permukaan dalam maupun luar
4) Bentuk benda kerja tidak harus tertentu
5) Toleransi penyelesaian dapat dipertahankan, sehingga hasilnya mampu tukar
6) Hasil pekerjaan nya dapat bersaing dengan produk permesinan lain nya
3. HAL-HAL PENTING SEBELUM MEMBESARKAN LUBANG
Perkakas pembuat lubang, berbeda dengan mesin perkakas lain nya, karena mesin perkakas umumnya dimaksudkan untuk pekerjaan atau operasi tunggal, sedangkan mesin pembesar lubang disiapkan untuk produksi massal. Fakta-fakta ini lah yang memaksa agar memiliki informasi selengkap-lengkapnya tentang pekerjaan, bahan dan mesin yang akan dipakai, sebelum pembesar lubang di aplikasikan.
Secara jelas, dibawah ini diterangkan hal-hal yang perlu diperhatikan/dipelajari sebelum sebuah mesin pembesar lubang digunakan:
a. Jenis material yang akan dibesarkan lubang nya
b. Ukuran dan bentuk pemotongan
c. Mutu penyelesaian yang diperlukan
d. Kekerasan benda kerja
e. Toleransi atau akurasi yang harus dipertahankan
f. Jumlah benda kerja yang akan diproses
g. Jenis mesin yang akan dipakai
h. Metode support untuk memegang alat pembesar lubang
i. Kekuatan maksimum benda kerja untuk menahan tekanan dari pembesar lubang